La formation plasturgie par la voie de l’apprentissage de l'INSA Strasbourg est une formation résolument orientée conception et production de pièces en polymère éco-conçues dans le cadre de l’usine 4.0, avec notamment un module de fabrication additive. Au cours de ce module de formation, les apprentis en 4ème année ont dû concevoir et produire le plus rapidement possible des composants fonctionnels.
Après une présentation des différents procédés de fabrication additive de pièces polymères et métalliques, les apprentis ont été confrontés à un projet, avec comme cahier des charges la conception d’un soufflet en silicone sur mesure.
Après une phase de conception du soufflet, les apprentis ont pu utiliser les moyens de fabrication additive de la plateforme Science des matériaux et ingénierie des surgaces (SMIS) de l’INSA Strasbourg, à savoir les différentes machines d’impression 3D de type FDM (traitement numérique de la lumière) et de type SLA (stéréolithographie) et les matériaux d’impression associés.
Au travers de ce projet, outre l’utilisation de moyens de prototypage rapide (FDM et SLA), les apprentis ont pu tester toutes les étapes numériques qu’impliquent ces nouvelles démarches de conception. Ils ont pu évaluer les effets de l’introduction de la fabrication additive pour accélérer le processus de conception, favorisant des modifications rapides et de fait l’aide à la décision et la validation finale du design au regard du cahier des charges fonctionnelles.
Modélisation puis fabrication par impression 3D
La figure 1 illustre la première phase, qui consiste à proposer une modélisation CAO (Conception assistée par ordinateur) du composant à produire, puis à le fabriquer par impression 3D le prototype en utilisant des matériaux de l’impression 3D non fonctionnel pour l’application visée.
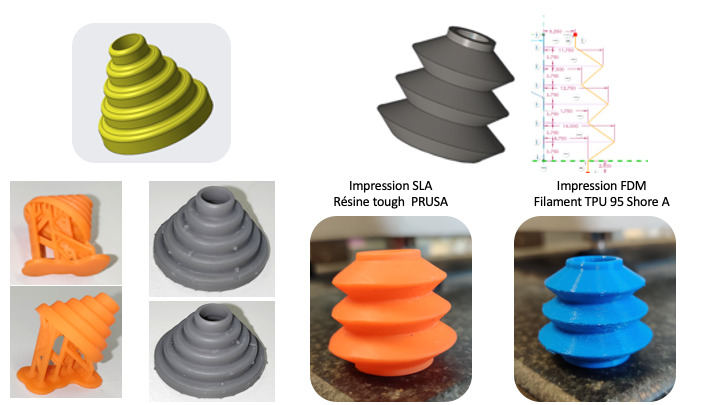
Figure 1 : exemples de conception de soufflet avec la phase de CAO, puis la production du prototype à l’aide de matériaux non fonctionnels soit par SLA, soit par FDM.
Ce prototype peut être contrôlé afin d’améliorer les paramètres d’impression ou encore de réaliser des modifications du design notamment pour une meilleure adaptabilité au procédé d’impression et ainsi éviter tout défaut de surface (rugosité) ou volumique (parois trop fines, formes mal définies, fissures ou déformations importantes). Concernant la maîtrise des états de surfaces, des solutions de parachèvement ont également été testées, après une optimisation des paramètres d’impression. La plateforme SMIS doit se doter dans les prochains temps d’un certain nombre de procédés de finition et de parachèvement des pièces produites par impression 3D.
Cette thématique est directement en lien avec le parcours Matériaux innovants et éco-respectueux, ouverts aux étudiants du département mécanique (génie mécanique, mécatronique et plasturgie) de l’INSA Strasbourg mais aussi aux étudiants de l’UFR de Physique & ingénierie de l’Université de Strasbourg inscrits dans le cadre du master Sciences et génie des matériaux – parcours Design de surfaces et matériaux innovants (DSMI).
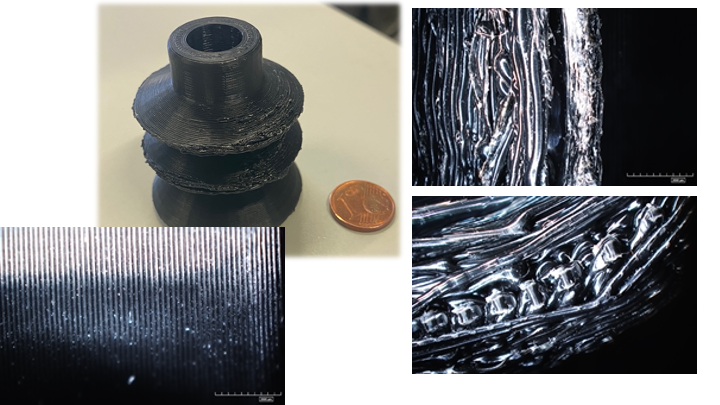
Figure 2 : analyse de la morphologie des composants produits par impression 3D avec un contrôle des dimensions fonctionnelles, des états de surface et enfin de la présence de défauts.
La dernière étape pour réaliser une pièce/un composant fonctionnel, notamment en utilisant le matériau d’intérêt (du silicone RTV 3325), les apprentis ont dû imaginer un outil, le concevoir en CAO et le réaliser par impression 3D. Une fois tous les éléments de l’outillage réalisés (figure 3), les étudiants ont produit des soufflets en silicone par coulée.
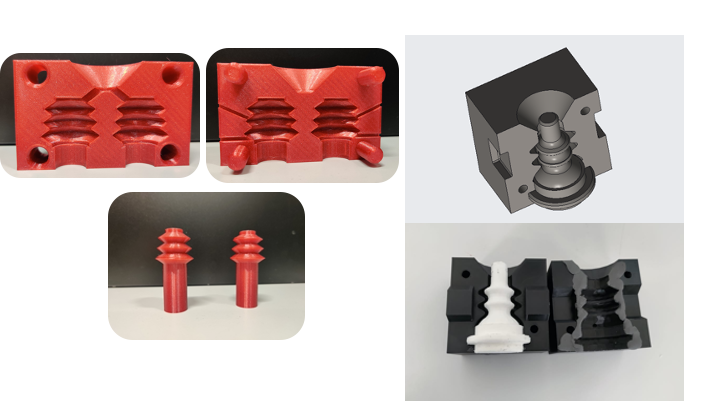
Figure 3 : Exemples d’outillages réalisés pour produire des soufflets en silicone sur mesure. Deux matériaux ont été utilisés pour réaliser en FDM les outillages, le PETG et l’ABS.
Ce projet a été le moyen de montrer aux apprentis que les moyens de fabrication additive ne sont pas parfois une fin en soi pour produire le composant. Les systèmes d’impression FDM ou SLA peuvent être « simplement » une étape dans le processus de conception (validation du design au regard des fonctions du composant).
Ces procédés peuvent être mis en œuvre pour la fabrication d’un outillage spécifique, qui permettra de mettre en forme une petite série de composants fonctionnels avec la répétabilité nécessaire à toute production (ce qui n’est pas forcément garanti avec une production directe par fabrication additive, dont la plupart des procédés FDM, SLA, et SLS sont très sensibles à un grand nombre de paramètres extérieurs).
Utilisation de l’impression 3D
L’utilisation de l’impression 3D pour la fabrication d’un outillage spécifique permet de réduire les temps de production depuis la conception jusqu’à la livraison aux clients. Cette approche permet à des procédés comme le moulage, la coulée sous vide, l’injection ou encore le thermoformage de s’adapter à la production de petites séries et donc la personnalisation de la production. Les outils produits par impression 3D pour ces procédés traditionnellement utilisés pour des productions de composants de grande masse, est souvent limitée à un certain nombre des pièces produites du fait d’une dégradation rapide en fonction du procédé plus ou moins sévère pour les surfaces actives de l’outillage (injection, thermoformage, coulée) mais aussi du matériau utilisé pour produire l’outillage.
En fonction de la quantité totale à produire, il est souvent nécessaire de produire plusieurs outillages en impression 3D, ce qui, dans la majorité des cas, reste largement inférieur au coût d’un outillage traditionnel, et garantit un coût unitaire compétitif.